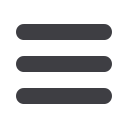
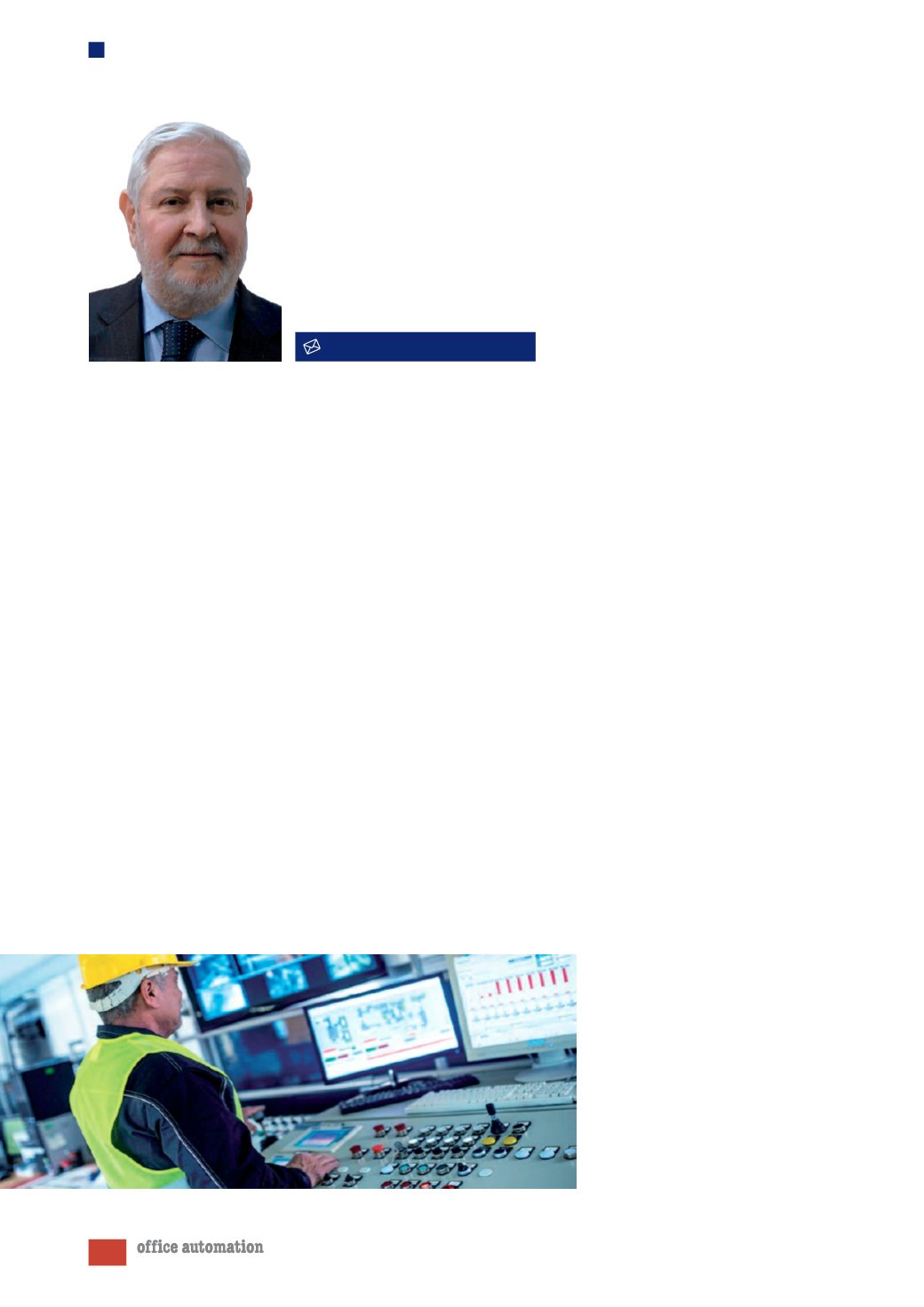
L’industria 4.0 è caratterizzata da una
decisa transizione negli ambienti pro-
duttivi dalle tecnologie analogiche alle
tecnologie digitali. Ovviamente, le tec-
nologie digitali erano già presenti nelle
fabbriche a partire dagli Anni ’70, ma
con Industria 4.0 il software assume
un’importanza predominante a tutti
i livelli, poiché è il cuore e il cervel-
lo delle principali tecnologie abilitanti
(Key Enabling Technologies – KET’s):
dal software embedded nelle macchine
utensili a controllo numerico, nei robot
e nei PLC che controllano i centri di
lavoro ai sistemi di gestione delle sup-
ply chain, dal firmware che controlla
sensori e oggetti intelligenti all’IoT e
al cloud, dai sistemi per il controllo di
qualità all’analisi dei big data.
In altre parole, il software si espande
sia a livello orizzontale, collegando e
integrando i vari silos applicativi delle
aziende (sistemi di progettazione, si-
mulazione, produzione, automazione,
logistica, sistemi gestionali, CRM, sistemi
direzionali, etc), sia a livello verticale,
scalando tutti i livelli della ‘piramide
della conoscenza’: dati, informazioni,
conoscenza, saggezza, come rappre-
sentata nella tabella.
Integrazione sempre più spinta
I principali tipi di software industria-
le sono i sistemi SCADA (Supervi-
sory Control And Data Acquisition),
DCS (Distributed Control System),
HMI (Human Machine Interface), MES
(Manufacturing Execution Syastem) e
MOM (Manufacturing Operation Ma-
nagement). In particolare i tradizionali
sistemi SCADA sono basati su sistemi
di elaborazione centralizzati mentre i
DCS sono basati su reti gerarchiche
di computer distribuiti (Edge Com-
puter). In pratica questa suddivisione
non esiste più poiché tutti i principali
sistemi SCADA sono in grado di gestire
qualsiasi combinazione di PLC, edge
computer, server locali e in cloud. I
produttori tradizionali di questi siste-
mi, come le multinazionali Bosch, GE,
Omron, Siemens, e le italiane Reply,
Progea e Copadata, entrano sempre
di più nel campo della progettazio-
ne, mentre le software house leader
nel campo della progettazione (CAD,
CAM, CAE, PDM, FEM) come Autode-
sk, Dassault, PTC e Altair si integrano
sempre più con la produzione, anche
grazie ai progressi fatti dal software di
macchine utensili CNC, stampanti 3D
e robot. Per esempio, Creo 4.0 di PTC
colma il divario tra CAD 3D e stampa
3D consentendo di progettare, otti-
mizzare, convalidare e stampare con
un unico software, e rende la proget-
tazione più intelligente consentendo
la creazione di strutture di reticoli uni-
formi controllate parametricamente,
la connessione diretta alle stampanti
3D, la convalida e gestione dei lavori
di stampa e la connessione diretta a
centri servizi esterni, se non si hanno
in azienda le tecnologie necessarie per
realizzare i prototipi o i prodotti finiti.
Autodesk e Altair puntano all’ottimiz-
zazione topologica e strutturale degli
oggetti prodotti con la stampa 3D e
nuove filosofie di progettazione come
il Design Generativo, mentre Dassault
eccelle nelle applicazioni di realtà vir-
tuale immersiva e aumentata. I pro-
duttori di networking e di piattaforme,
IL SOFTWARE PER L’INDUSTRIA 4.0
DAI PLC AI BIG DATA
90
giugno 2017
Giancarlo Magnaghi
Consulente
g.magnaghi@studiomagnaghi.itINDUSTRIA 4.0