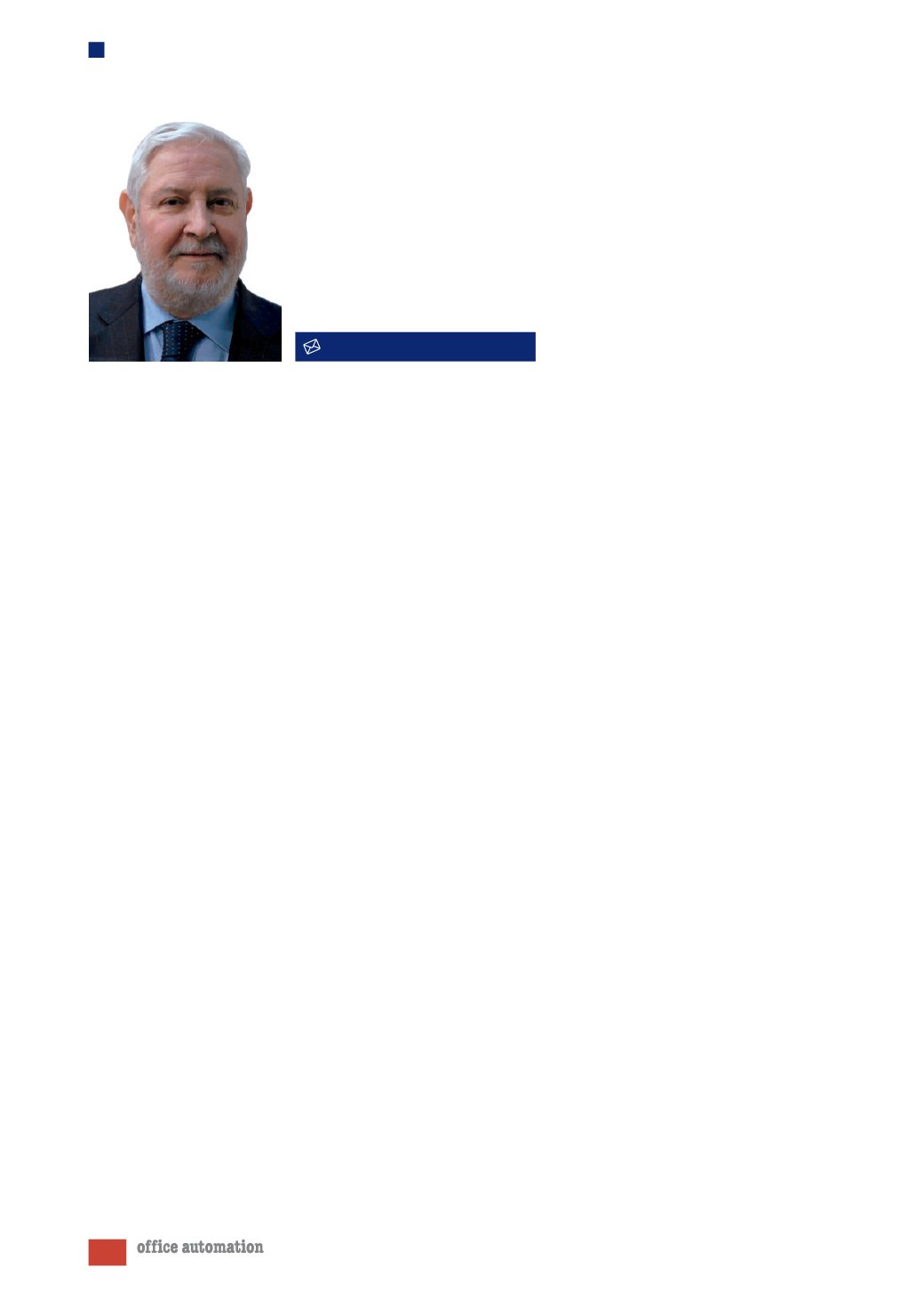
L’era industriale, che iniziò in Inghil-
terra circa 200 anni fa e poi si estese
rapidamente negli Stati Uniti, in Giap-
pone e nei maggiori Paesi dell’Europa
continentale, si è evoluta attraversan-
do varie fasi di maturazione chiamate,
come sappiamo,‘rivoluzioni industriali’.
La prima rivoluzione industriale, che
iniziò alla fine del ‘700 con le macchi-
ne a energia idraulica e poi a vapore,
durò oltre un secolo.
La seconda rivoluzione industriale, a
cavallo tra ‘800 e ‘900, sfruttò la diffu-
sione dell’energia elettrica, del petrolio
e dei motori a combustione interna
per iniziare la produzione di massa
tramite le catene di montaggio di au-
tomezzi, elettrodomestici e altri pro-
dotti di grande serie.
La terza rivoluzione industriale, nei
primi Anni ’70, fu caratterizzata dall’u-
tilizzo dell’elettronica e dell’informatica
per controllare la produzione, in un
primo tempo a livello di singole mac-
chine a controllo digitale (macchine
utensili a controllo numerico, robot di
produzione), poi collegate nelle pri-
me celle di produzione automatizzate.
La strada verso l’automazione
Già nel 1974 fu concepito il primo
modello concettuale di fabbrica com-
pletamente automatizzata grazie a una
gerarchia di controlli automatici a loop
chiuso (fabbrica a luci spente), che già
delineava le principali caratteristiche
delle odierne smart factory (ovvero
fabbriche intelligenti), e fu coniato per
la prima volta il termine CIM nel libro
Computer Integrated Manufacturing
di Joseph Harrington, ma rimase let-
tera morta fino alla metà degli Anni
’80 poiché le tecnologie non erano
sufficientemente mature ed econo-
miche: gli operai lavoravano in molti
casi ancora meglio delle macchine e
i benefici in termini di riduzione dei
costi non erano sempre apprezzabili
vista proprio la scarsa resa di diversi
processi automatizzati.
Nella prima metà degli Anni ’90,
nell’ambito dei programmi Esprit (Eu-
ropean Strategic Program on Rese-
arch in Information Technology) del-
la Comunità Europea, fu sviluppata
l’architettura di riferimento CIMOSA
(CIM Open SystemArchitecture) che
definiva i primi standard europei per
i sistemi CIM.
A par tire dal 2012, quasi vent’anni
dopo, questo modello è stato ripreso
in Germania e denominato “Industrie
4.0”, adeguandolo alle nuove tecno-
logie e ai nuovi modelli di business, e
oggi che si sta estendendo anche ai
maggiori Paesi industrializzati di tutto
il mondo, in Italia dall’anno scorso, si
parla comunemente di ‘Industry 4.0’.
Questo modello descrive una fabbri-
ca intelligente e un modo di produrre
intelligente (smart manufacturing) ba-
sato su una rete integrata di sistemi
di produzione che comprende i se-
guenti elementi.
1. Un’automazione sempre più spinta
in tutti i campi di applicazione gra-
zie a sistemi sempre più intelligenti,
autonomi e in grado di apprendere
(machine learning).
2. L’utilizzo di nuovi sistemi di proto-
tipazione (stampa 3D) e di produ-
zione (AM) integrati con gli impianti
esistenti (CNC, robot) per con-
sentire maggiore agilità e flessibilità
nella produzione e quindi maggio-
re personalizzazione di massa dei
prodotti industriali.
3. Un elevato livello di interconnessio-
ne e comunicazione tra dispositivi e
sensori (RFID, M2M, IoT), tra com-
puter, tablet e smartphone (cloud
computing), tra uomini e macchine
(M2H, HMI), tra uomini e uomini
(H2H), attraverso reti private locali
o geografiche o tramite Internet
(IoE).
4. Sistemi di visione artificiale, realtà
aumentata e virtuale, simulazione
di processi.
5. Reti di sensori distribuiti nell’am-
biente (sensor cloud, smart dust),
nelle macchine e negli indumenti
(wearable computing), per acquisire
enormi quantità di dati (Big Data)
che consentono varie applicazioni
SMART MANUFACTURING, COME
CAMBIA IL MODO DI PRODURRE
L’EVOLUZIONE DEI PROCESSI DI PRODUZIONE E LE RIVOLUZIONI INDUSTRIALI
92
gennaio-febbraio 2017
Giancarlo Magnaghi
Consulente
g.magnaghi@studiomagnaghi.itINDUSTRIA 4.0